One of the major considerations companies will have when selecting a case former and sealer is whether they are going to use tape or glue to seal the boxes. Every application is different, and there are no one-size-fits-all rules to dictate which one would be the better fit. However, there are some factors that would generally point you in one direction or the other.
Tape
A big reason people choose a tape seal is because they have a lower level of output. The start-up cost with a tape sealer is much lower because businesses only need to purchase a tape head and not the tank, hoses and guns required for gluing. Lower speed applications are also not as impacted by the more hands-on approach required by using tape. To replace a tape roll, the machine needs to be stopped as the rolls are changed out and then started back up again.
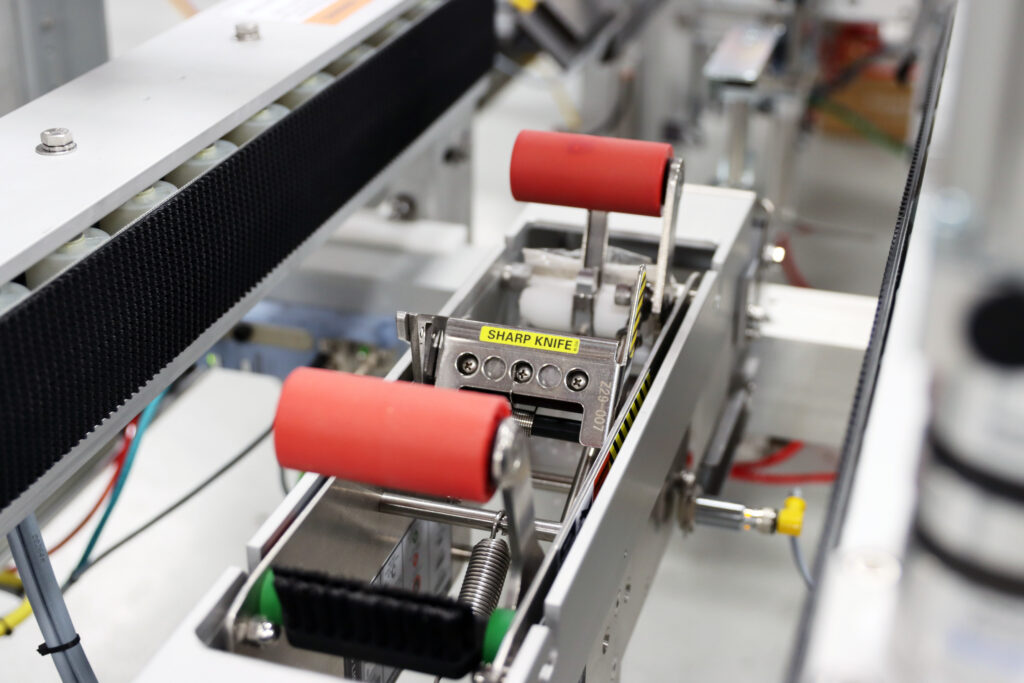
Another situation in which tape is often the better choice is in more hands-on work environments due to safety. Both options present risk of injury, with burns from hot glue guns and cuts from the tape cutter blade requiring caution from the operators. Burns, however, are much more common than cuts, making tape the safer choice for a line with more employee interaction, especially with less experienced staff. Tape also tends to require less maintenance in these machines than glue, another benefit for companies with inexperienced team members who may not have the in-depth knowledge required to fix issues that come up.
What’s going into the box is also a factor. If the product does not provide a lot of support inside of the box, the machine will not have the pressure it needs to compress glue dots. This results in a lot of larger manufacturers opting for tape with products like potato chip bags or maybe under filled applications.
Glue
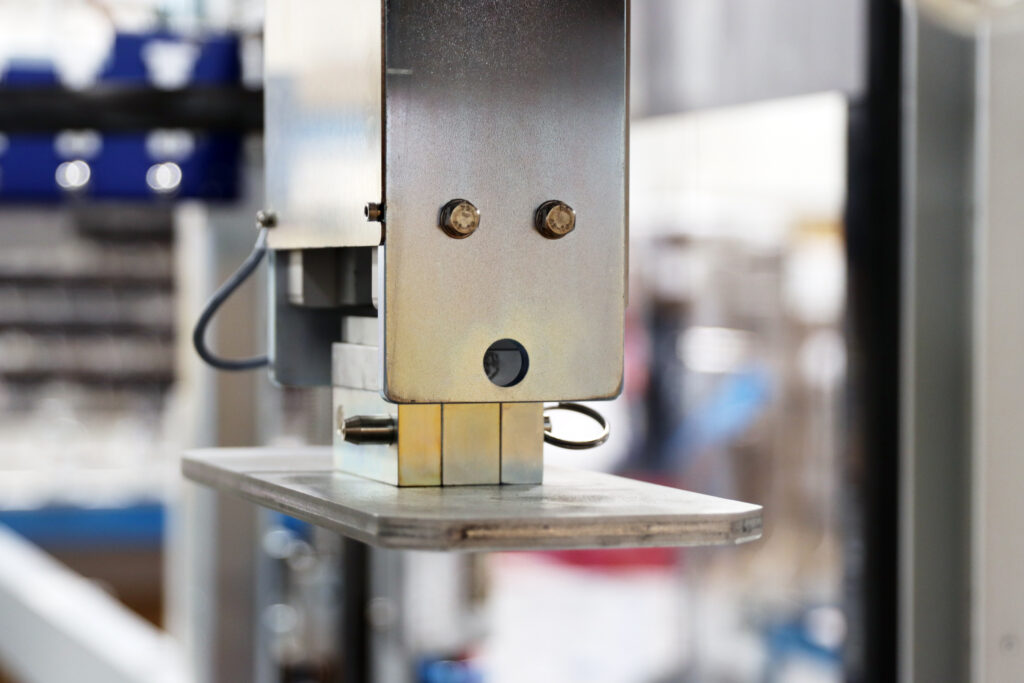
Glue is generally the sealing method of choice for companies that package a higher volume of products. Though the upfront costs are higher for glue, companies will see greater savings over the long term. Using glue can be up to three times less expensive than using tape per case sealed. Employees can also fill the glue tank as the machine is running, reducing stoppages. For larger companies with high volumes, these savings quickly add up and offset the initial cost difference. Additional savings can come from the bonds themselves. With glue, the major flaps are locked on the minor flaps, creating a much more rigid and secure box than a tape seal. This is especially true in more humid environments where tape has more trouble sticking. Neither sealant has significant instances of cases coming unsealed, but it happens even less frequently when glue is used instead of tape.
Glue can also give operations more flexibility. The omni fold bin style is an option that can only be used with glue. Similarly, tray formers are either self-locking or use glue; there is no tape option. With this flexibility, companies may also opt for cases with shied flaps, which reduces the amount of corrugated needed per box, providing further savings.
These are just some of the details that can help you determine whether tape or glue is the right choice for you. Talk to a Wexxar Bel representative to work on building a personalized case forming solution to boost your efficiency and improve your operation.
Mark Greever is the National Account Manager for Wexxar Bel (https://www.wexxar.com/). He can be reached at Mark.greever@promachbuilt.com.